Business Areas
Nano CVD Coating
Combining nanotechnology with products from various fields creates synergy and improves performance.
We have cutting-edge Nano CVD Coating technology that can create synergies by combining products in various fields to improve their performance. By combining nano coating technology and semiconductor wafer coating technology, it can be applied to various industries such as semiconductors, medical devices, bio, aerospace, and electronic components. We will always evolve to become a company that provides cutting-edge technology that is ahead of others in order to create differentiated value for our customers.
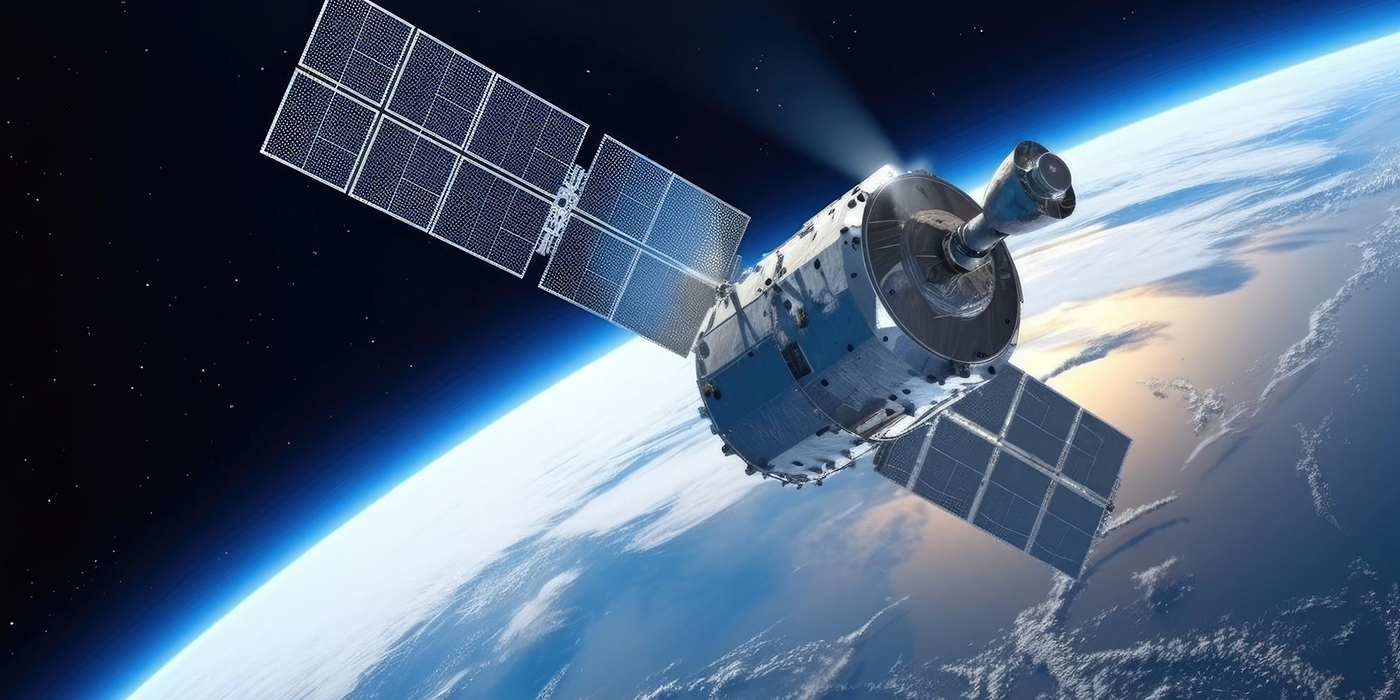
Parylene Coating
Parylene Coating is a technology that provides nano coatings with stable quality.
Because this technology is vacuum deposited in the gas phase, it can solve problems such as shape deformation or surface shrinkage that occur with solution coating. Nano coating forms a uniform coating between microscopic gaps or structures through surface polymerization in the gas phase. Through this, it forms a protective film on the surface of various parts such as electronic products, communication equipment, mechanical parts, and medical devices, providing functions such as insulation, corrosion prevention, waterproof coating, and powder scattering prevention. Nano-coating can evenly coat products to enhance protection and increase stability and durability. Thanks to these properties, nanocoatings are used in many industrial sectors as excellent protection solutions.
Prorietary technology, Ultimate result
Experience the power of innovation with world-class nanocoating technology!
Business Point
Ultra-thin, superior coating provides excellent functionality.
Applicable Industries
Applicable industries
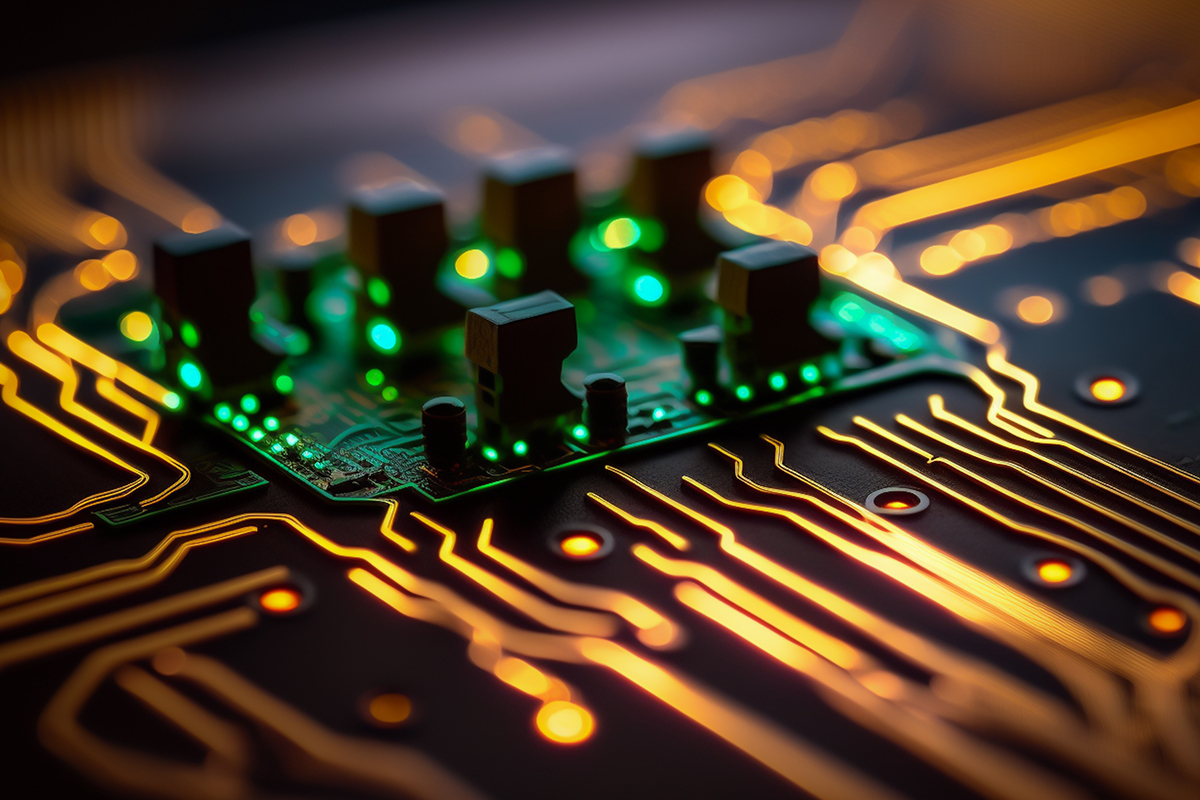
Circuit Boards
- Coating with no shape restrictions and very thin thickness
- Chemical-resistant and stable against mold attack
- Good adhesion and enhanced insulation and solder joints
- Formation of uniform coating layer
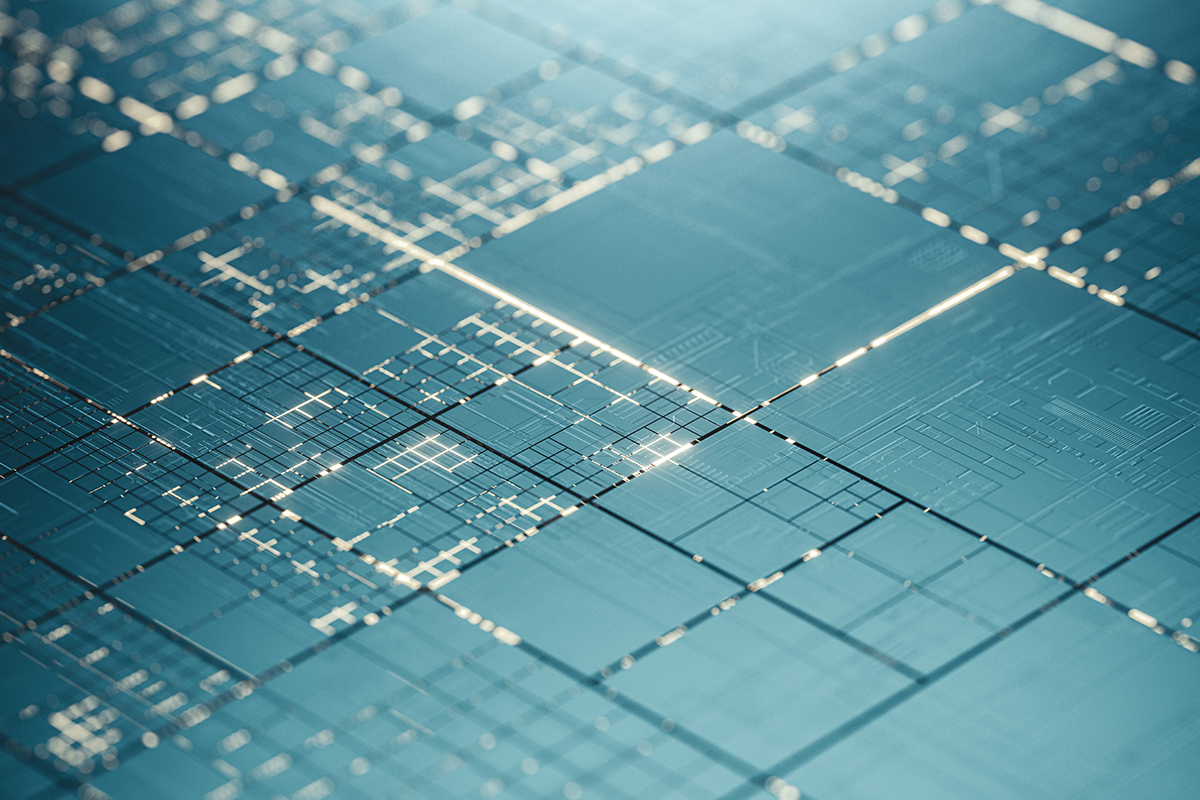
Hybrid Circuit
- Adhesion suitable for ceramic materials
- Coating possible even in narrow spaces of 10 ㎛
- Reinforced Wire bonds
- Fixation of solder balls and foreign matter particles
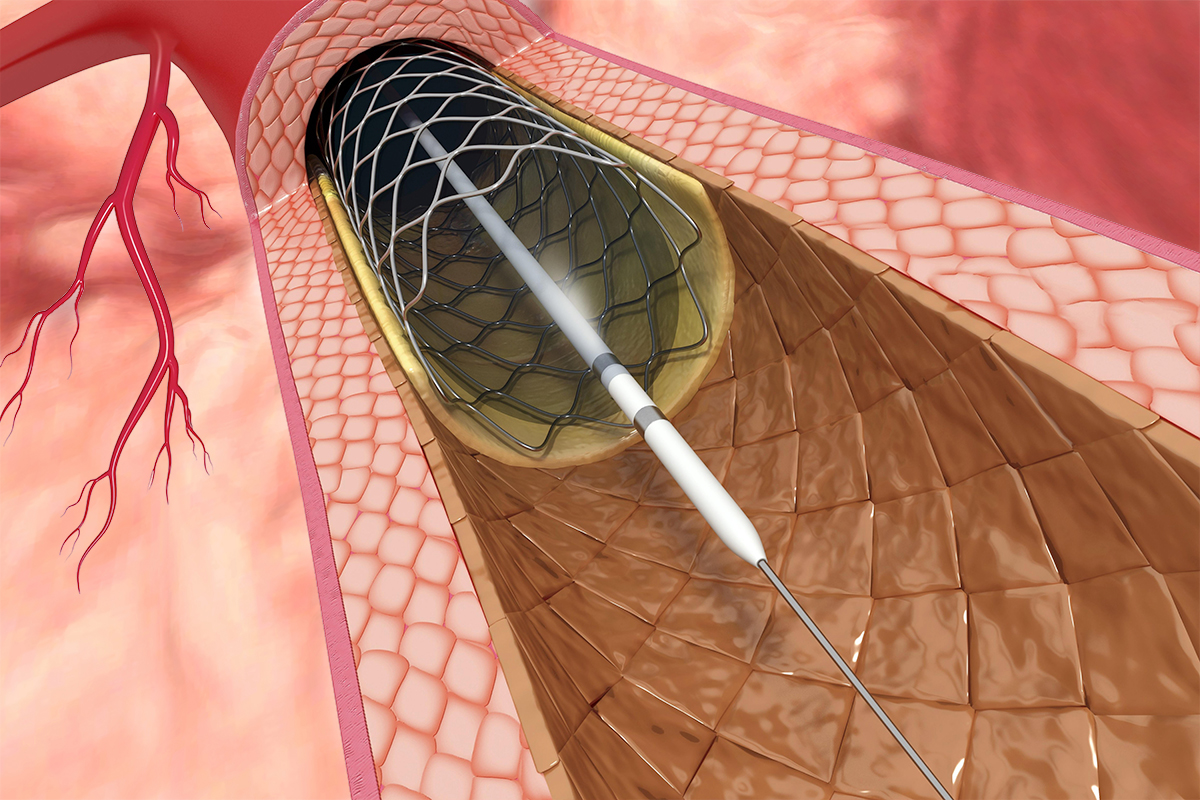
Medical Components
- Protecting the body from toxic materials materials
- Coating for surface lubricity of catheters, endoscopes, etc.
- Heart Stents
- Electrosurgical tools
- Needles and epidural probes
- Medical electronics
- Pacemarkers
- Difibulators
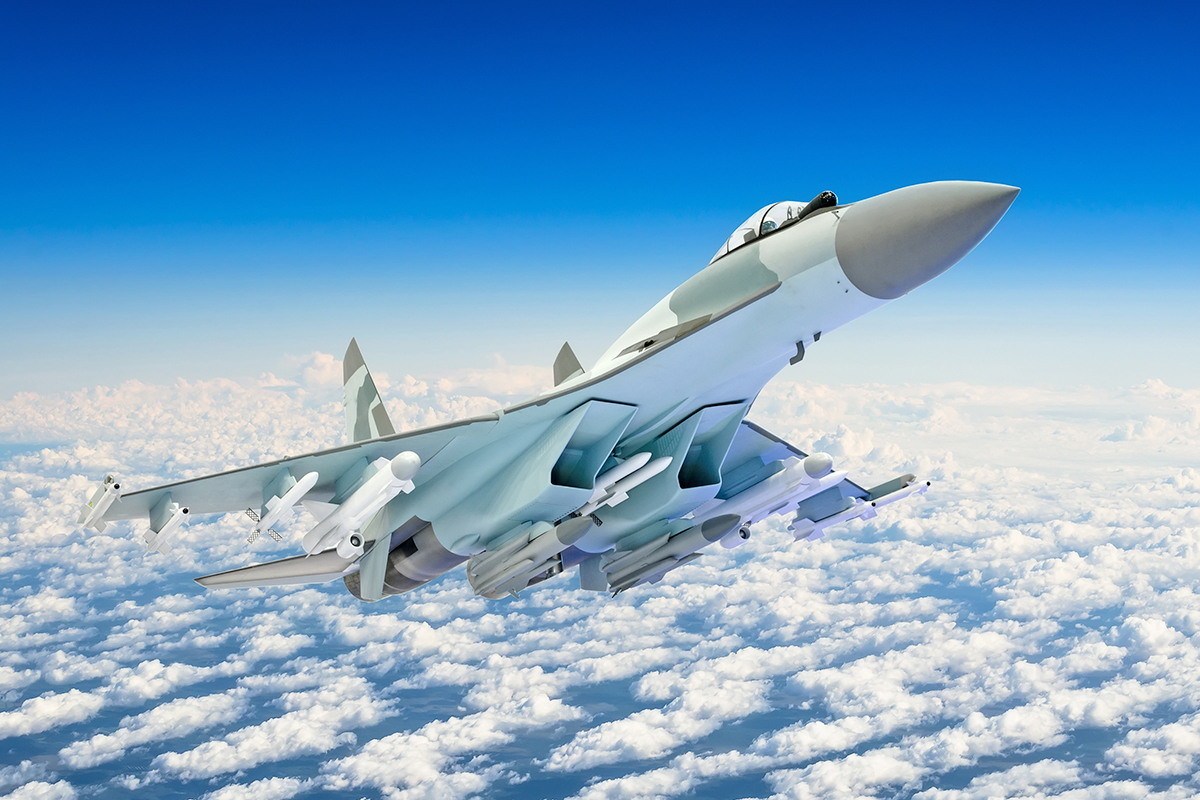
Military & Defense Applications
- Weapons & Munition systems
- Ground, Air and Aerospace vehicles
- Robotic devices
- Radar devices
- Navigation devices
- Wearable devices
- Field devices
- Unmanned aircraft and Aerospace platform
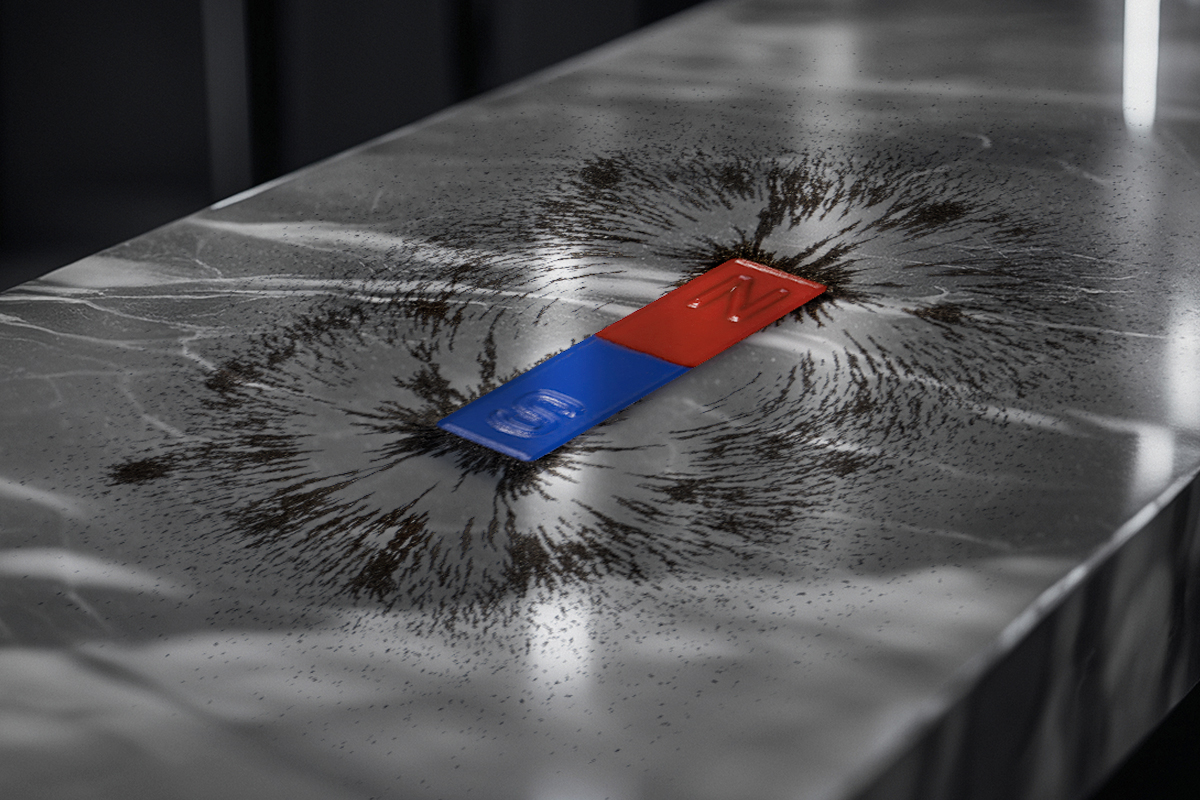
High Risk Electronics & PCB Conformal Coating
- SMT and Hybrid Circuit Assemblies
- Lead Free Coating
- Precision Sensors
- MEMS
- Motor Assembles
- Flexible Circuits and PCB Conformal Coating
- Silicon Wafers
- Ferrites